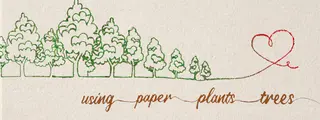
Making paper is both high-tech and simple. High-tech because of the way trees are processed to create wood pulp, the substance paper is made of, while supporting the circular economy and giving back to the earth. And simple because it involves a natural, renewable material, trees, which are replanted or regenerated as they’re harvested for use.
The result? An array of papers that accompany you through your life, whether that’s helping you relax with a coloring book or organizing important family documents.
Following is a look at how paper is made, from cultivation of flourishing forests through delivery of products, from the companies at the heart of it.
What Is Paper Made Of? What Materials?
Most paper is made from the cellulose fiber found in trees. While the majority of timber harvested in the U.S. is used for things like home construction and furniture, approximately 36% is used to make paper and paperboard. Both wood and wood byproducts, such as branches, as well as sawmill residues and recycled paper go into making the pulp that ultimately becomes paper.
For more detail on paper pulp and papermaking machines, read on.
What Is Paper Pulp? And How Is Paper Pulp Made?
Paper pulp is basically what paper is made of: wood fiber from trees. (There are papers from other materials, such as cotton, but those are specialty papers, not the paper that you depend on every day.)
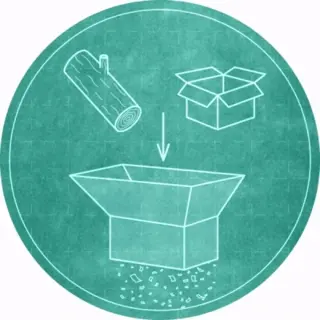
At paper mills, the wood is stripped of its bark, as bark can’t be used in paper. (Don’t worry—the bark doesn’t go to waste. It’s combined with other residue to provide most of the steam and electricity required for a mill’s operations, making paper a part of the circular economy.) The wood that remains is then ground or sliced into tiny pieces so that it can be pulped.
There are two primary types of pulping: mechanical and chemical pulping. With mechanical pulping, the lignin—an organic chemical that helps hold tree fibers together—stays in the pulp. The end result is a less durable, rapidly aging “groundwood” paper. Mechanical pulp is used for paper that is meant for shorter-term use, such as newsprint.
Chemical pulp begins the same way, with groundwood fibers. But from there, papermakers introduce a chemical into the pulp to separate the lignin from the wood fibers. The mixture is put into a pressure cooker that breaks down into pulp and a liquid known as “black liquor.”
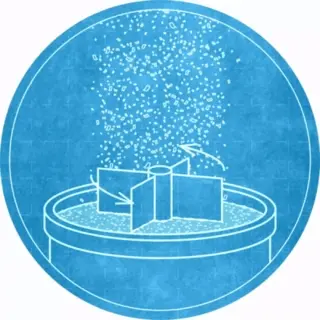
From there, washers remove the black liquor, and the chemicals are recovered and saved to be used in the next batch, helping cut down waste. Up to 95% of the original cooking chemicals are recovered each time for reuse. That’s marvelous! The end result is a pulp that’s lighter in color and with stronger fibers. This makes it especially appropriate for high-quality applications such as letter-writing paper.
Don’t be misled by the washing, though: More than 90% of the water used to make paper is cleaned and returned to the environment, and U.S. paper mills have cut water use by 50% since 1975.
One note: The process above is used for new paper, or “virgin” paper. But because paper is one of the most recycled materials in the United States, we also encounter paper made from recycled materials every day. So when you recycle any paper—virgin paper or recycled paper—you’re contributing to paper’s sustainability. Recycled paper is made by churning used paper with water to create a different sort of pulp than virgin paper requires. But from there, the process is much the same for both types of paper.
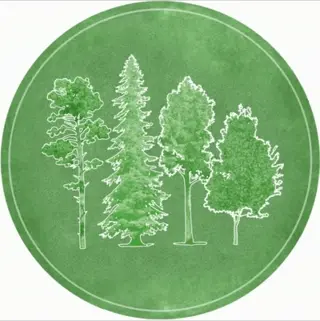
What Trees Are Used to Make Paper?
Papermakers in the U.S. rely heavily on softwood trees such as pines, firs, spruces and larches because their longer fibers produce stronger paper, especially for use in packaging. Other trees used in papermaking include oak, maple, hickory, hemlock, aspen and birch trees. Their shorter fibers are better for smoothness and printability.
Most trees that are turned into paper are purpose-planted, and the paper industry harvests just what it needs, mostly from private lands whose stewards grow trees for this purpose and then replant or regenerate what is harvested. In fact, papermakers always grow more than they harvest, contributing to the more than 1 billion trees that are planted in the U.S. each year.
How Does a Papermaking Machine Work?
Before the first papermaking machine was invented in 1799, paper could only be produced in single sheets. But once machinery entered the picture, papermaking could become a larger industry.
The basics of a papermaking machine: Once the pulp solution is ready, it’s placed onto a wire screen where some of the water used to make it is drained and vacuumed away, generating a thick web of damp, fibrous material. That web is pressed to remove even more water, then passed over huge drying cylinders, resulting in paper that is then wound onto giant reels weighing 40 tons or more.
Want to go deeper into how paper is made? Dive into the machinery.
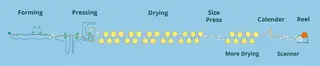
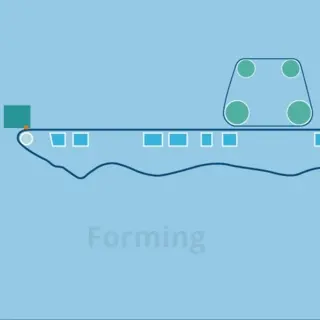
Sections of a Papermaking Machine
Paper machines usually have four main sections: the wet end, the wet press section, the dryer section, and the calendar section. Together, these form the fibers, press the wet fibers, dry them, and make them smooth—in other words, into paper. Fun fact: Papermaking machines can stand as high as a three-story building and extend as long as three football fields in length!
Steps of the Papermaking Process
Raw materials (pulp, water, and additives) are poured into the headbox at the wet end. After being blended together, the liquid mass is extruded onto a porous, continuous belt that massages the fibers into uniformity. The direction, flow, and speed of machine result in most fibers aligning in the same direction—that’s where a piece of paper gets its grain, allowing it to be torn and folded more easily in one direction than in the other. On the forming belt, some of the water is drained and vacuumed away but it’s still 75% water at that point.
In the wet press section, the still damp mat transfers onto a synthetic fabric belt between rollers that progressively press out more water. It’s about 60% water content at that point. From there, the web goes into the dryer section to remove additional moisture. By the time it’s finished in the dryer, paper may have a moisture content between 3% and 5%. Corrugated containerboard values average between 7.5% to 9% moisture content.
The last step is the calendering process, which irons the paper between a stack of chrome-plated rollers to increase uniformity, smoothness, and gloss. After that, the paper is slit and wound into individual shipping rolls, wrapped and made ready to head out the door for cutting to size, packaging, shipping and other final processes for customers such as retailers and publishers.
Sustainable Forestry and Papermaking
For paper and packaging companies, thriving, sustainable forests are the key to survival. So their health has to be prioritized in every step of production.
Sustainable forestry is about stewardship and care—care for trees, naturally, but also for smaller plants, soil, wildlife and water. It creates a mutually supportive relationship between nature and people, which help renew and sustain the resources we depend on.
Sustainability has been the backbone of the paper industry for decades, and we couldn’t do what we do without it. Choosing paper is one way to show support for healthy forests because U.S. paper producers work with private landowners to purposely grow and maintain them.
Today, one-third of the U.S. is forested. That’s nearly 766 million acres, and private forests contribute to more than half of it.
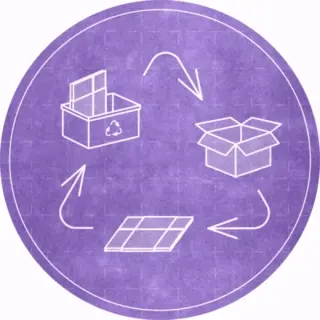
Recyclability of Paper
Recycling gives paper products as many as seven lives, based on the number of times they can be recycled, which makes paper one of the planet’s most sustainable resources. Once consumers buy the paper products and use them, most can be recycled. The possibilities include everything from printer paper to mail, cereal boxes, shipping cases, paper bags and more. And advancements in treatments and coatings are rapidly increasing the repulpability of finished paper products. Yes, pizza boxes, paper cups, sandwich wraps, and produce boxes are now often recyclable.